- Intralogistik
- Automatisierung
Wann lohnt sich Lagerautomatisierung? Kosten, ROI, Entscheidung
Ob sich Lagerautomation rechnet, hängt von Kosten, Prozessen und Wachstum ab. Artikel zeigt ROI‑Logik, Schwellen und Alternativen.
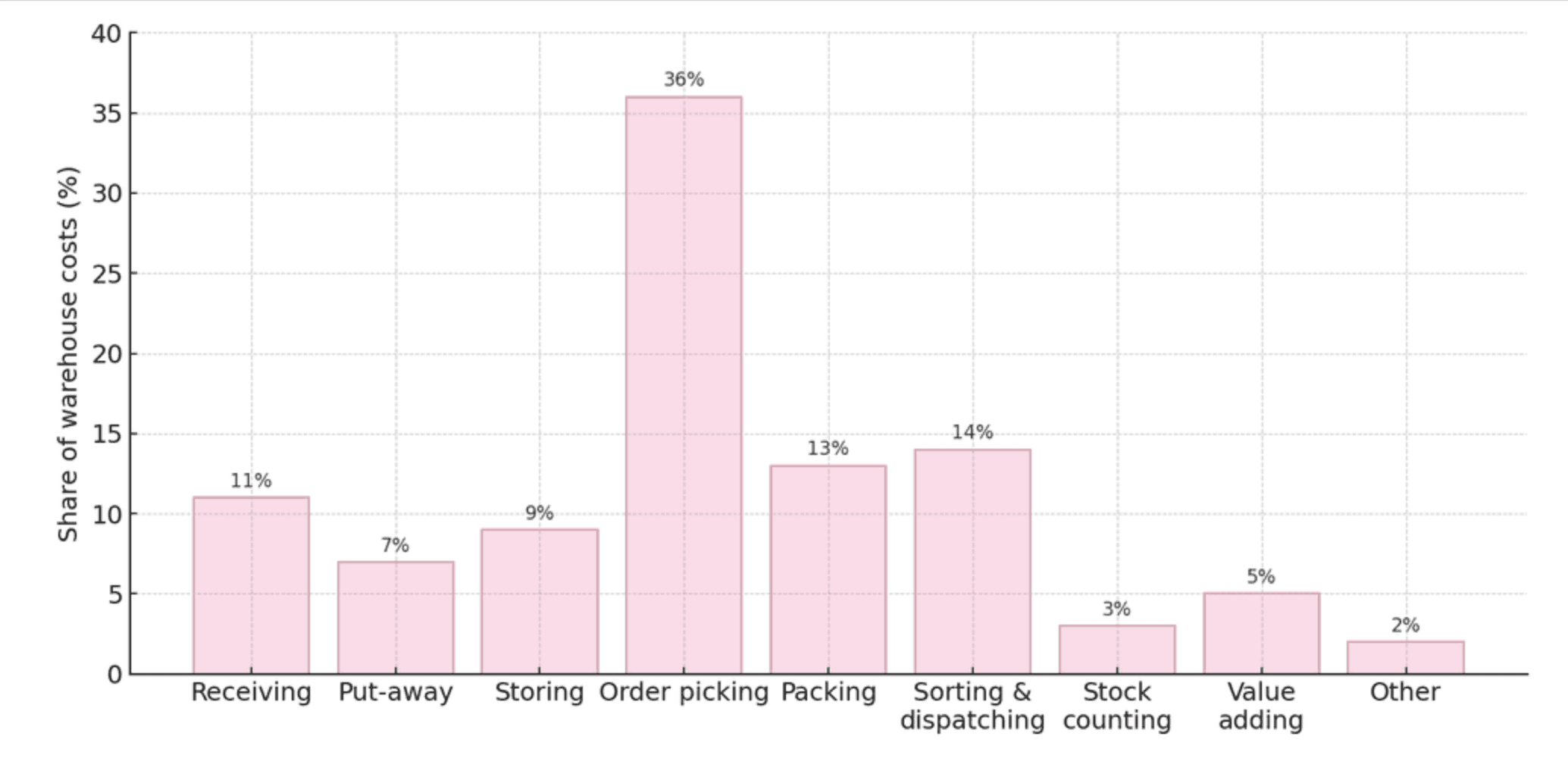
In a nutshell: Automatisierung lohnt sich oft erst ab bestimmten Schwellenwerten – meist ab rund 1.000 Picks pro Tag oder mehr als 2 000 SKUs. Rechnet man die Gesamtkosten (TCO) über einen Zeitraum von mehreren Jahren, wird die Technik oft zum klaren Kostenvorteil, sofern vor‑ und nachgelagerte Prozesse (Wareneingang, Versand) mithalten. Bleiben Volumen niedrig oder konzentrieren sich viele Picks auf wenige Artikel, sorgt ein gut organisiertes, manuelles Fachbodenlager weiterhin für die flexibelste und günstigste Lösung.
Viele Lager fragen sich, ab wann man in ein automatisiertes System investieren sollte. Die Entscheidung hängt von ROI‑Zielen, Durchsatz, SKU‑Zahl, Fehlerkosten sowie Personal‑ und Flächenverfügbarkeit ab. Klassische „Mann‑zur‑Ware“-Konzepte stoßen bei wachsender Vielfalt und steigendem Volumen an Grenzen; Automatisierung muss sich jedoch kalkulatorisch lohnen.
Wirtschaftliche Faktoren: ROI und Kostenvergleich
Ein zentraler Aspekt ist die Wirtschaftlichkeit. Automatisierte Lagersysteme erfordern meist hohe Investitionskosten (für Anlagen, Software, Implementierung), wohingegen ein manuelles Lager mit Regalen und Mitarbeiter:innen zunächst geringere Fixkosten verursacht oder im Brownfield bereits vorhanden ist. Dem gegenüber stehen bei der Automation langfristig niedrigere operative Kosten: weniger Personalaufwand, geringere Fehlerkosten und optimalere Flächennutzung. Return on Investment (ROI) und Amortisationszeit sind hier wichtige Kennzahlen. Generell werden bei sinnvollen Automatisierungsprojekten ROI-Zeiträume von unter fünf Jahren angestrebt, wobei in vielen Fällen sogar Amortisation innerhalb von drei Jahren erreicht wird. Als Daumenregel kann man annehmen, dass sich die Investition idealerweise in 2–5 Jahren durch Einsparungen zurückverdienen sollte.
Kostenstruktur: In manuellen Lagern ist der Personaleinsatz oft der größte Kostenblock – das Kommissionieren allein kann über 55 % der operativen Lagerkosten ausmachen. Steigende Löhne (z. B. +11 % pro Jahr im Schnitt in den USA zuletzt) und Personalknappheit erhöhen diese Kosten zusätzlich. Automatisierung zielt darauf ab, diesen variablen Kostenblock zu senken und durch anfängliche Investitionen zu ersetzen, die sich über die Zeit auszahlen.
Ein weiterer Kostenfaktor sind Fehlkommissionierungen: Studien zeigen, dass in manuellen Prozessen die Kommissioniergenauigkeit oft nur bei ~97 % liegt (d. h. rund 3 % Fehlerrate). Jede falsche Lieferung verursacht im Schnitt etwa 19,50 € an Folgekosten (Korrektur, Retouren, Administratives). Bei hohem Auftragsvolumen summieren sich solche Fehlerkosten erheblich, weshalb Automation – mit einer höheren Genauigkeit (Propagiert werden oft >99 % Pick-Genauigkeit) – hier finanzielle Vorteile durch Fehlervermeidung bringt.
Auch Flächenkosten spielen hinein: Zusätzliche Lagerhallen oder Regale bedeuten Miete bzw. Abschreibung; automatisierte Systeme können durch höhere Lagerdichte Fläche sparen und so Kosten senken.
Kostenbeispiel: Manuell vs. Vertikallift
Um die Überlegungen greifbar zu machen, betrachten wir ein Beispiel. Die folgende Tabelle vergleicht ein manuelles Kleinteilelager mit einem automatisierten System (z. B. Vertikallifte) auf Basis von ca. 1.000 Picks pro Tag. Dabei wurden für beide Varianten die selben Leistungsanforderungen unterstellt.
Anmerkung: Ohne zusätzliche Kontrolle würden die Fehlerkosten im manuellen Szenario direkt ~152.000 € jährlich betragen. Durch Einsatz einer Qualitätskontrolle (Personalkosten ~28.600 €) kann die Fehlerquote jedoch auf ~1 % gedrückt werden, womit die Fehlerfolgekosten weitgehend vermieden werden. Die Tabelle vergleicht das manuelle Lager inkl. dieser Qualitätsmaßnahme mit dem automatisierten Lager, sodass beide ca. 99 % Genauigkeit erreichen.</small>
Dieses vereinfachte Beispiel veranschaulicht die ökonomischen Effekte: In der automatisierten Lösung halbiert sich der Personalaufwand, die Fehlerkosten entfallen nahezu, und sogar Mietfläche wird eingespart. Pro Kommissionierposition sinken die Gesamtkosten von rund 0,60 € (manuell) auf 0,24 € (automatisiert), in diesem Szenario. Unterm Strich ergibt sich eine jährliche Kostenersparnis von ~92.000 € – die Investition amortisiert sich in etwa anderthalb Jahren. Natürlich variiert die genaue ROI-Rechnung je nach Auslegung des Systems, Lohnniveau und individuellem Prozess; doch ein deutlicher Kostenvorteil zeigt sich meist ab einem gewissen Skalierungspunkt. Unternehmen sollten daher frühzeitig kalkulieren, ab welchem Durchsatz und Kostenniveau ein automatisches Lagersystem break-even erreicht. Faustregel: Je höher die laufenden Kommissionierkosten (Personal, Fehler, Platz) im Ist-Zustand und je größer das erwartete zukünftige Volumen, desto eher rentiert sich die Automatisierung.
Operative Anforderungen: Volumen, Vielfalt und Prozessqualität
Neben der reinen Kostenrechnung spielen prozessuale Anforderungen eine entscheidende Rolle. Hier geht es um Fragen wie: Wie viele Artikel und Aufträge müssen täglich bewältigt werden? Wie komplex ist der Prozess? Wie hoch sind die Anforderungen an Geschwindigkeit und Genauigkeit?
Durchsatz & Bestellfrequenz: Hohe Auftragsvolumen und Peak-Zeiten sind ein klassischer Treiber für Automatisierung. Wenn ein Lager täglich nur wenige dutzend Aufträge bearbeitet, lässt sich das manuell effizient bewältigen. Steigt die Belastung jedoch auf Hunderte oder gar Tausende von Picks pro Tag, wächst der Personalbedarf überproportional und die Prozesse können zum Engpass werden. Automatisierte Systeme erreichen hier eine andere Leistungsfähigkeit. Durch paralleles Arbeiten (mehrere Quellspeicher gleichzeitig anfahrbar, automatische Sequenzierung etc.) lassen sich Spitzen abfangen, die manuell nur mit zusätzlichen Arbeitsstunden zu bewältigen wären. So kann z. B. ein einzelner „Goods-to-Person“-Arbeitsplatz die Arbeit von 4–5 manuellen Kommissionierern übernehmen. Zudem können automatische Anlagen – einmal installiert – rund um die Uhr laufen, auch nachts oder am Wochenende, was mit rein manueller Kommissionierung (gebunden an Arbeitszeiten) nicht möglich ist. Aber Achtung: Hier muss man natürlich auch vor- und nachgelagerte Prozessschritte bedienen oder puffern können. Diese permanente Verfügbarkeit erlaubt es dann, Engpässe zeitlich zu entzerren und Aufträge kontinuierlich abzuarbeiten. In Branchen mit engen Lieferzeitfenstern (Same-Day / Next-Day Delivery Anforderungen) kann dies ein spannender Vorteil sein.
Artikelanzahl & Sortiment: Die SKU-Anzahl (Artikelvielfalt) beeinflusst, wie komplex ein Lager zu organisieren ist. Bei nur wenigen Artikelarten und begrenzter Lagerkapazität ist ein manuelles System oft völlig ausreichend und am flexibelsten. Sobald jedoch tausende von SKUs gemanagt werden müssen, geraten traditionelle Fachbodenregale an Effizienzgrenzen. Viel Artikelauswahl bedeutet in manuellen Lagern längere Such- und Wegzeiten für das Personal und erhöht die Notwendigkeit einer durchdachten Lagerplatzoptimierung (Slotting). Automatisierte Kleinteilelager spielen ihren Vorteil aus, indem sie das Sortiment softwaregestützt verwalten und den Mitarbeitern gezielt vorsortiert bereitstellen.
Prozessqualität & Fehlerquoten: Wie bereits im Kostenkapitel angedeutet, sind Genauigkeit und Qualität wesentliche Kriterien. Hohe Fehlerraten in der Kommissionierung bedeuten unzufriedene Kunden, Retouren und Zusatzkosten. Manuelle Prozesse sind anfälliger für Pickfehler (falscher Artikel, falsche Menge) – teils liegen Inventurgenauigkeiten nur bei ~66 % in durchschnittlichen Lagern, was auf menschliche Fehler und Prozesslücken zurückzuführen ist. Automatisierte Systeme können hier Abhilfe schaffen: Sensoren, Scanner und Software prüfen laufend die Entnahmen, sodass Fehlgriffe nahezu, aber nicht gänzlich, eliminiert werden. Dadurch reduzieren sich nicht nur die direkten Fehlerkosten, sondern auch indirekte Aufwände (z. B. weniger Kundenreklamationen, geringerer Kontrollbedarf). Wenn also in Ihrem aktuellen Lager die Fehlerquote spürbar zur Problemzone wird – etwa weil der Prozess sehr hektisch ist – kann Automatisierung einen Qualitätssprung bringen.
Geschwindigkeit & Servicegrad: Schließlich spielt die geforderte Durchlaufzeit eine Rolle. Müssen Aufträge „just in time“ oder innerhalb weniger Stunden kommissioniert und versandt werden, stoßen manuelle Prozesse schnell an personelle Limits. Automatisierte Lager können sehr kurze Durchlaufzeiten gewährleisten, da sie Wartezeiten (z. B. Lagermitarbeiter auf dem Weg zum Regal) minimieren.
Auch wenn es darum geht, gleichzeitige Bestellungen mit vielen Positionen fehlerfrei zusammenzustellen, bieten automatisierte Systeme durch ihre Softwaresteuerung einen Vorteil. Kurz gesagt: Wenn Schnelligkeit und Zuverlässigkeit des Fulfillments Kernanforderungen sind, tendiert die Waage in Richtung Automation.
To Do: Regelmäßig die Kennzahlen des Lagers prüfen. Wenn die Kosten je Kommissionierung steigen und manuelle Abläufe an Performance-Grenzen gelangen, sollte man über Automatisierung nachdenken. Bleibt aber jedoch ebenso ehrlich, in welchen Bereichen ein einfaches manuelles System unschlagbar ist. So stellt man sicher, dass die Lagerlogistik optimal auf die Bedürfnisse des Geschäfts abgestimmt ist – heute und in Zukunft.
Ressourcen und Skalierung: Personal & Fläche als Entscheidungskriterien
Die Verfügbarkeit von Mitarbeitern sowie die vorhandene Lagerfläche sind weitere kritische Faktoren bei der Frage „Automatisieren oder nicht?“.
Personalkosten und -verfügbarkeit: Lagerautomatisierung wird häufig durch die Personalthematik getrieben. In vielen Lagern gibt es bereits einen Fachkräftemangel, der die Personaldecke dünn macht – laut ILO stieg der Arbeitskräftemangel in der Logistik 2022 um 25 % an. Gleichzeitig steigen die Löhne und Gehälter für Lagerpersonal kontinuierlich. Dies setzt Unternehmen unter Druck, mit begrenztem Personal immer mehr Leistung zu erbringen. Automatisierung bietet einen Ausweg, indem sie die Abhängigkeit von menschlicher Arbeitskraft reduziert. Wenn es in der Region schwerfällt, genügend qualifizierte Lagermitarbeiter zu finden (oder zu halten), oder wenn Überstunden und Leasingkräfte zur Norm werden, lohnt ein Blick auf Automatisierung. Wichtig ist allerdings zu bedenken, dass automatisierte Anlagen oft selbst Spezialisten brauchen – etwa für Wartung und Steuerung. Doch unterm Strich lässt sich durch geeignete Technologie der Bedarf an einfachen Kommissioniertätigkeiten deutlich senken. Dies wirkt auch dem Thema Arbeitsbelastung und Ergonomie entgegen: Monotone oder körperlich anstrengende Picks (z. B. schwere Teile aus hohen Regalen holen) können Maschinen übernehmen, was Arbeitsunfälle reduziert und personelle Ausfälle durch Verletzungen oder Ermüdung vorbeugt. Die fundamentale Motivation hinter dem Automatisierungsboom ist denn auch, die steigenden Arbeitskosten in den Griff zu bekommen und den Betrieb skalierbarer zu machen.
Flächenrestriktionen und Lagerkapazität: Ein oft unterschätzter Auslöser für Automatisierungsprojekte ist der Platzmangel. Wenn die vorhandene Lagerfläche nicht mehr ausreicht, stehen Entscheidungen an: zusätzliche Hallen anmieten, anbauen – oder durch Technik mehr aus dem bestehenden Raum herausholen. Automatisierte Lagersysteme glänzen meist mit deutlich höherer Lagerdichte. Beispielsweise können automatische Regalsysteme Gänge stark reduzieren oder ganz eliminieren, was eine maximale Ausnutzung der Grundfläche erlaubt. Fahrzeuge, Roboter oder Shuttles erreichen Produkte in engen Kanälen oder mehrgeschossigen Strukturen, in die kein menschlicher Bediener so effizient gelangen könnte. Dadurch lässt sich oft vertikal bauen und die Raumhöhe besser ausnutzen als mit manuell bedienten Regalen. Wenn also die Lagerfläche zum Engpass wird und ein kostenintensiver Ausbau droht, kann Automation die Alternative sein: Viele Firmen stellen fest, dass sie mit automatischen Kleinteilelagern oder Hochregalen die Lebensdauer ihres aktuellen Lagerstandorts verlängern können, anstatt sofort in einen Neubau zu investieren.
In Zeiten, in denen Lagerfläche teuer und knapp ist (Europaweite Verfügbarkeitsrate teils unter 3 %), ist dieser Faktor nicht zu vernachlässigen.
Zusammengefasst: Wenn Personal zur Engpassressource wird oder die Fläche aus allen Nähten platzt, verschiebt sich der Schwellenwert zugunsten einer Automatisierung. Umgekehrt gilt: Solange ausreichend Platz vorhanden ist und Arbeitskräfte günstig und verfügbar sind, fehlt ein wichtiger Druck, der die Investition rechtfertigt. Die Entscheidung muss immer unter Betrachtung aller Ressourcen erfolgen.
Wann eine manuelle Kommissionierung vorteilhaft bleiben kann
Trotz aller Vorteile automatisierter Lösungen gibt es zahlreiche Szenarien, in denen ein manuelles Lager (z. B. Fachbodenregalanlage mit „Mann-zur-Ware“-Prinzip) die bessere oder pragmatischere Wahl ist. Hier einige typische Fälle, in denen eine manuelle Kommissionierung Vorteile bietet:
- Geringe Artikelvielfalt und Volumen: In einem kleinen Lager mit überschaubarer SKU-Anzahl und niedrigem Durchsatz lohnt sich der Aufwand und die Komplexität einer Automatisierung meist nicht. Bei wenigen SKUs und keiner absehbaren Expansion ist ein manuelles Lagersystem oft ideal geeignet – es ist kostengünstig, simpel und absolut ausreichend dimensioniert. Die Fixkosten bleiben gering, und jeder weitere Artikel kann unkompliziert im Regal untergebracht werden.
- Hohe Zugriffsfrequenz auf wenige Artikel: Wenn sich viele Picks auf wenige Lagerplätze konzentrieren, kann das manuelle Picken effizienter sein – insbesondere, weil keine Wartezeiten für Behälterbereitstellung entstehen. Gleichzeitig ist der Aufwand, Behälter im automatisierten System für häufige Zugriffe ständig neu zu befüllen, vergleichsweise hoch. Ein guter Indikator: Je häufiger ein Behälter bereitgestellt wird, bevor er geleert ist, desto eher lohnt sich eine Automatisierung. Umgekehrt gilt: Wird der Behälter schon nach wenigen Picks wieder gewechselt, spricht das eher für ein manuelles System.
- Stark schwankende oder saisonale Nachfrage: Betriebe mit ausgeprägten Saisongeschäften (z. B. zu Weihnachten) oder sehr volatilen Bestellmengen schätzen die Flexibilität manueller Systeme. Personal kann je nach Aufkommen rauf- oder runtergefahren werden – etwa durch Einstellen von Temporärkräften in Peak-Zeiten. Diese Skalierbarkeit nach oben ist ein Vorteil des Menschen: Bei Auftragsspitzen lassen sich einfach mehr Leute zum Picken einsetzen. Automatisierte Systeme haben zwar oft hohe Kapazitätsreserven, sind aber dennoch fixe Systeme, die bei Unterauslastung weiter Abschreibung und Betriebskosten verursachen. Ein manuelles Lager kann man dagegen in schwachen Phasen einfach „leer stehen lassen“ bzw. mit Minimalbesetzung fahren, ohne dass Maschinen ungenutzt Kapital binden. Kurz: Bei unscheren, schwer prognostizierbaren Aufkommensmustern bleibt man mit manueller Kommissionierung flexibler. Erforderlich ist aber ein passender einfacher Prozess um temporäre Arbeitskräfte schnellstmöglich auf Leistung zu bekommen.
- Hohe Sortimentsdynamik und Änderungsbedarf: Wenn sich das Sortiment ständig ändert (z. B. Modekollektionen, saisonale Artikelwechsel) oder die Prozesse im Lager im Fluss sind, ist Flexibilität Trumpf. Automatisierte Systeme sind typischerweise weniger anpassungsfähig an geänderte Anforderungen – Umbauten oder Anpassungen sind teuer und aufwändig. Ein manueller Lageraufbau mit Standardregalen lässt sich hingegen schnell umorganisieren, falls z. B. neue Produktgruppen kommen oder Lagerzonen umgestaltet werden müssen. Auch beim Launch ganz neuer Artikel (mit unbekanntem Absatz) fährt man mit einem manuellen Setup risikoärmer, da keine spezifische Technik vorbereitet werden muss. Ein Lager mit sehr großer Artikelvielfalt und schneller Sortimentsrotation profitiert häufig mehr von der Flexibilität des manuellen Kommissionierens. Veränderungen im Geschäft lassen sich ohne lange Vorläufe adaptieren.
- Unhandliche oder spezielle Artikel: Nicht jede Ware eignet sich für die automatisierte Handhabung. Sehr sperrige, schwere oder empfindliche Artikel können in Standard-Automatiklagern Probleme bereiten. Beispielsweise stoßen autonome Roboter bei Gewichten, Abmessungen oder Formen außerhalb bestimmter Toleranzen an Grenzen. Ein manuelles Fachbodenregal ist hier oft besser, weil es universell für alles genutzt werden kann – vom Ersatzteil über die Matratze bis zum Gefahrgut. Wenn Ihr Lagergut also sehr heterogen ist oder besondere Handhabung erfordert (z. B. Glas, Chemikalien, etc.), behalten manuelle Lösungen ihre Daseinsberechtigung, da sie sich nicht auf bestimmte Maße beschränken. Gegebenenfalls kombiniert man auch: Die „gängigen“ Artikel laufen über eine Anlage, während Sondermaße manuell gelagert werden.
- Begrenztes Budget / Unklare ROI-Perspektive: Automatisierung muss finanziell gestemmt werden können. Ist das Investitionsbudget knapp oder der Business Case unsicher (z. B. weil das künftige Volumen schwer abzuschätzen ist), kann es sinnvoll sein, vorerst manuell zu bleiben. Ein traditionelles Lager ist leichter schrittweise optimierbar (z. B. erst bessere Software einführen, dann bei Wachstum eventuell Teilautomatisierungen hinzufügen). Man vermeidet damit das Risiko, sich durch eine große Investition zu früh festzulegen. In manchen Fällen können auch halbautomatische Lösungen ein Mittelweg sein – etwa Pick-by-Voice oder beleglose Kommissionierung – um Effizienzen zu heben, ohne gleich das ganze Lager umzubauen.
Zusammengefasst: Ein manuelles Lager punktet immer dann, wenn Einfachheit und Flexibilität wichtiger sind als maximale Effizienz. Geringe Mengen, hohe Anpassungsanforderungen oder spezielle Rahmenbedingungen sind klassische Gründe, vorerst beim manuellen Kommissionieren zu bleiben. Die Technik der Fachbodenregale ist bewährt, günstig und leicht zu bedienen – das sollte nicht aufgegeben werden, solange sie die Anforderungen erfüllt.
Manuelle Kommissionierung: Unterschätzt, aber mit Potenzial
Die manuelle Kommissionierung im Fachbodenregal wird in der Diskussion um Lagerautomatisierung oft vorschnell als ineffizient oder veraltet abgetan. Doch das greift zu kurz. Mit gezielten Maßnahmen lässt sich auch ein klassisches „Mann-zur-Ware“-System deutlich leistungsfähiger gestalten – bei gleichzeitig niedriger Komplexität und Investition.
Effizienzsteigerung im manuellen Lager
- Wegeoptimierung: Tourenplanung, Zonenbildung, Multi-Order-Picking
- Technische Assistenzsysteme: Pick-by-Scan, Pick-by-Voice oder Pick-by-Light
- Softwareeinsatz: Lagerverwaltungssoftware mit intelligenter Lagerplatzvergabe (Slotting)
- Layoutverbesserung: Schnelldreher ergonomisch platzieren, kurze Wege für ABC-Artikel
- Arbeitsplatzgestaltung: Ergonomische Pickstationen, Greifhilfen, klare Beschriftung
- Qualitätssicherung: Kontrollwiegung, Stichproben, Feedbacksysteme
- Schulung & Motivation: Mitarbeitende durch Kennzahlen sensibilisieren und einbinden
Solche Maßnahmen können die Pickleistung pro Mitarbeiter spürbar steigern und gleichzeitig Fehlerquoten reduzieren – ohne dass ein komplexes automatisiertes System erforderlich ist. In vielen Fällen lassen sich damit 80–90 % der Automatisierungsziele erreichen – zu einem Bruchteil der Kosten.
Zudem bleibt das System extrem anpassungsfähig: Neue Produkte, neue Kundenanforderungen oder kurzfristige Änderungen lassen sich schnell umsetzen. Das manuelle Lager wird so zu einem leistungsfähigen und robusten Rückgrat, gerade für wachsende oder dynamische Unternehmen.
Zusammenfassend : Wer manuell kommissioniert, ist nicht automatisch ineffizient. Oft mangelt es nicht an Technik, sondern an Prozessdisziplin, guter Führung oder geeigneter Unterstützung. Eine professionalisierte manuelle Kommissionierung ist kein Widerspruch – sondern in vielen Fällen ein unterschätztes Potenzial.
Fazit
Den geeigneten Zeitpunkt für die Einführung eines automatisierten Lagersystems zu bestimmen, erfordert eine ganzheitliche Betrachtung. Kalkulatorische Überlegungen (Kostenvergleich, ROI) bilden die Basis jeder Entscheidungsfindung – die Investition muss sich mittelfristig lohnen. Gleichzeitig müssen die Prozesse und Mengen im Lager so beschaffen sein, dass eine Automatisierung ihre Stärken ausspielen kann (hoher Durchsatz, komplexes Sortiment, Bedarf an Geschwindigkeit und Genauigkeit). Schwellenwerte wie Anzahl SKUs, Bestellfrequenz oder Kommissionierkosten pro Auftrag dienen dabei als Anhaltspunkte, keine starren Regeln. So kann z. B. ab einigen tausend Auftragspositionen pro Tag und mehreren tausend Lager-SKUs eine Automatisierung immer attraktiver werden – vor allem in Verbindung mit hohen Arbeitskosten oder Platzproblemen. Umgekehrt gilt: Bei niedrigem Volumen und hoher Ungewissheit fährt man mit manuellen Prozessen oft besser.
Eine ehrliche Bewertung umfasst auch die weichen Faktoren: Wie wichtig ist Flexibilität? Wie sieht die Wachstumsprognose aus? Steht ein Unternehmenswandel bevor, der vielleicht erst Prozesse stabilisieren muss, bevor Automation Sinn ergibt? All diese Fragen fließen in den „Fahrplan“ zur Automatisierung ein. Häufig ergibt sich der richtige Zeitpunkt dann, wenn das Lager unter den bestehenden Methoden an Grenzen stößt – sei es durch Kostendruck, Leistungsdefizite oder äußere Umstände (Arbeitsmarkt, Immobilienmarkt). Automatisierung kann dann erhebliche Vorteile bringen: mehr Effizienz, weniger Fehler, skalierbare Leistung und Entlastung der Mitarbeiter. Voraussetzung ist jedoch, dass sie passgenau geplant wird und zum Profil des Unternehmens passt.
Am Ende steht idealerweise eine fundierte Entscheidung: Automatisieren ja oder nein – und wenn ja, wann? Diese Entscheidung will gut vorbereitet sein. Mit einer gründlichen Analyse der genannten Kriterien und gegebenenfalls Pilotprojekten lässt sich der optimale Zeitpunkt bestimmen. Eines ist sicher: Die Technologie im Lagerbereich entwickelt sich rasant weiter, und die Investitionshürden sinken teilweise (z. B. durch Robotics as a Service-Modelle). Doch egal ob vollautomatisch oder manuell – entscheidend ist, dass das Lager den aktuellen und zukünftigen Anforderungen gerecht wird. Eine Automatisierung zur richtigen Zeit kann ein echter Game-Changer sein, während sie zum falschen Zeitpunkt leicht zum Fehlinvestment wird.