- Hardware
- Intralogistik
- Planung
- Automatisierung
Das AutoStore-System im Detail: Komponenten, Partner, Planung – ein Leitfaden für Entscheider
AutoStore verstehen: Alles über Roboter, Ports, Planung und Integratoren – für Logistikleiter, IT-Verantwortliche und Projektplaner
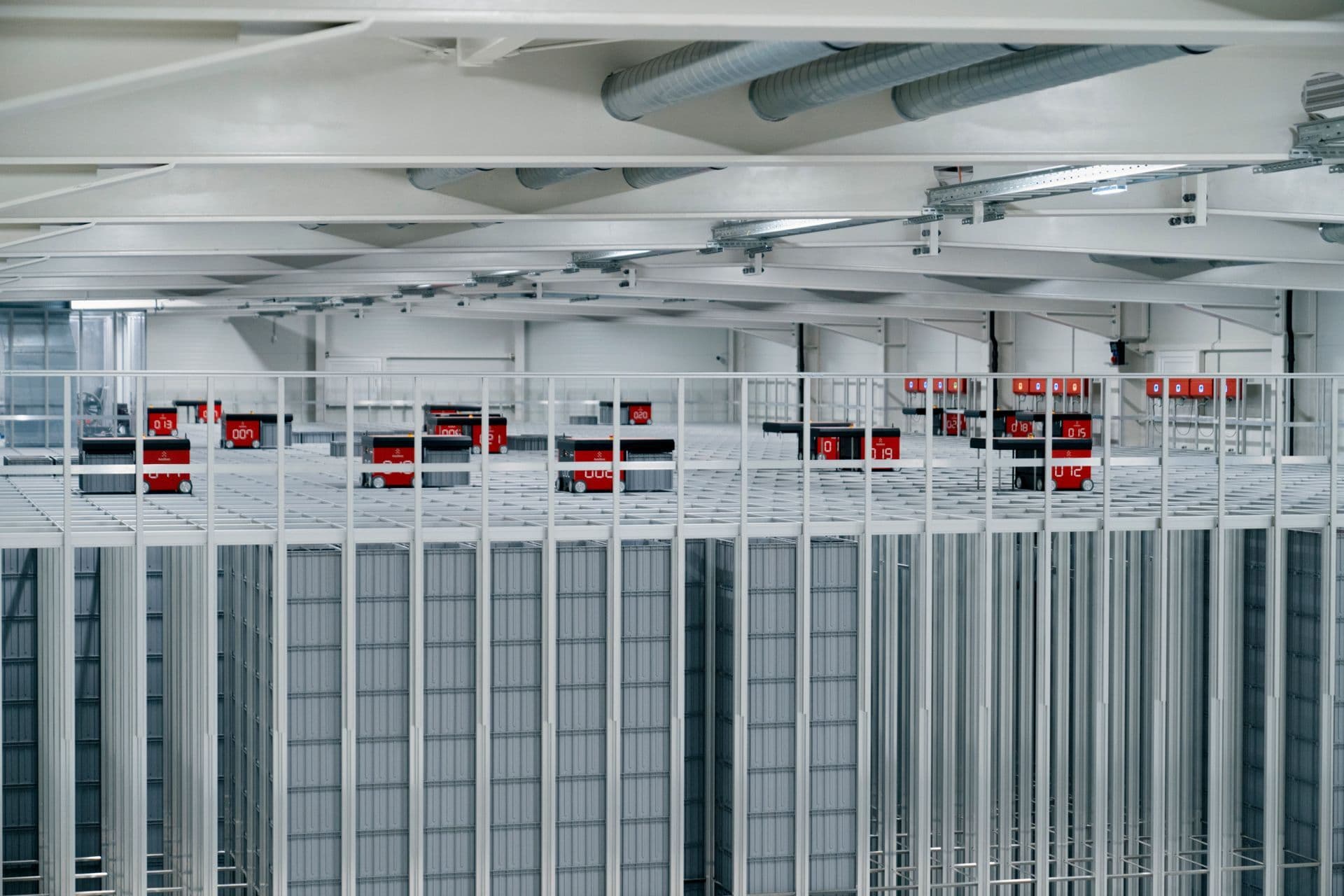
AutoStore™: Entwicklung, Leistungskennzahlen, Vergleiche und Integration in der Lagerlogistik
In a nutshell: AutoStore™ ist ein automatisiertes Lager- und Kommissioniersystem in Cube-Storage-Bauweise, das in der Intralogistik für Effizienzsteigerung und Platzersparnis sorgt. Das System hat sich in den letzten Jahren rasant verbreitet und gilt inzwischen als Benchmark für automatisierte Kleinteilelager. Insbesondere im E-Commerce und in der Ersatzteillogistik in der ganzen Welt setzen Logistikleiter auf AutoStore, um den wachsenden Anforderungen an Durchsatz und Liefergeschwindigkeit gerecht zu werden. Dieser Fachartikel beleuchtet die Historie und Entwicklung von AutoStore, präsentiert Leistungskennzahlen des Systems, stellt offizielle Integrationspartner vor und zeigt ergänzende Technologien auf, die häufig in Kombination mit AutoStore zum Einsatz kommen.
Entwicklung und Historie von AutoStore™
AutoStore wurde 1996 in Norwegen von Jakob Hatteland und Ingvar Hognaland gegründet. Hognaland, inspiriert vom Rubik-Würfel, entwickelte das Konzept eines kubischen Lagerautomatens, um ungenutzten Luftraum in Lagerregalen zu eliminieren – anstelle klassischer Regale werden Behälter übereinander in einem Grid gestapelt und von Robotern ausgelagert. Nach mehreren Jahren Entwicklungsarbeit und einem erfolgreichen Prototyp begann Hatteland 2004 mit der Kommerzialisierung des Systems über ein Netzwerk ausgewählter Vertriebs- und Integrationspartner. Dieses Partnermodell erwies sich als effektiv: AutoStore wuchs zunächst in Nordeuropa und verbreitete sich ab den 2010er-Jahren weltweit.
Ein Meilenstein war die internationale Expansion ab 2011, als erste Installationen in Zentral- und Westeuropa, Nordamerika und Asien realisiert wurden. Heute ist AutoStore global präsent und zum De-facto-Standard für automatisierte Kleinteilelagerung avanciert. Mit aktuell rund 1.550 installierten Systemen bei über 1.000 Kunden weltweit ist AutoStore Marktführer im Bereich der kubischen Kleinteilelagerung. In über 50 Ländern – darunter zahlreiche Anlagen in Deutschland, Österreich und der Schweiz – hilft AutoStore Unternehmen, ihre Lagerprozesse zu modernisieren. Die Bedeutung dieser Erfindung wurde 2023 gewürdigt, als die Gründer Hatteland und Hognaland in die Logistics Hall of Fame aufgenommen wurden. AutoStore hält über 1.600 Patente und hat damit die Lagertechnik nachhaltig geprägt.
Wie funktioniert das AutoStore-System?
AutoStore ist ein automatisiertes Lager- und Kommissioniersystem für Kleinteile, das auf einem würfelförmigen Aluminium-Grid basiert. In diesem Raster werden Behälter (sogenannte Bins) vertikal gestapelt ohne dass klassische Regalgänge erforderlich sind. Die Oberfläche des Grids dient als Fahrfläche für autonome Roboter, die einzelne Behälter anheben, umschichten und zu Übergabepunkten transportieren.
Ablauf eines typischen Lagerprozesses im AutoStore
- Identifikation des Lagerorts
Bei einem Lagerabruf erhält das AutoStore-System vom übergeordneten Lagerverwaltungssystem (WMS) die Information, welcher Artikel benötigt wird. In vielen Implementierungen wird AutoStore vom WMS als ein einziger Lagerbereich betrachtet. Die genaue Verortung der Artikel innerhalb des Grids – also in welchem Bin sich welcher Artikel befindet – erfolgt durch die AutoStore-eigene Steuerungssoftware. Diese verwaltet die Zuordnung der Artikel zu Behältern und kennt deren exakte Position im System. - Zugriff durch Roboter
Roboter auf der Grid-Oberfläche übernehmen den Zugriff auf den Zielbehälter. Liegt dieser nicht zuoberst, werden die darüberliegenden Bins temporär entfernt und auf benachbarten Feldern zwischengelagert. Anschließend wird der benötigte Bin aufgenommen und zum nächsten freien Port gebracht. - Übergabe am Port
Die Roboter liefern den Behälter an eine Entnahmestation – sogenannte Ports. Dort erfolgt die Kommissionierung durch Mitarbeitende oder eine Übergabe an nachgelagerte Automatisierungslösungen. Nach Abschluss wird der Behälter in das Grid zurückgeführt.
Lagerlogik und Systemverhalten bei Rücklagerung
AutoStore führt keine explizite Lagerplatzoptimierung im klassischen Sinn durch. Vielmehr ergibt sich die Verteilung der Artikelpositionen aus dem Ablauf der Zugriffe. Wird ein Artikel benötigt, heben die Roboter ihn aus dem Grid – nach der Entnahme wird der Bin anschließend oben aufgestapelt.
Dadurch entsteht ein natürlicher Effekt:
- Häufig genutzte Artikel befinden sich tendenziell näher an der Oberfläche, weil sie öfter bewegt und damit immer wieder oben abgelegt werden.
- Seltener benötigte Artikel bleiben langfristig weiter unten, da sie nur selten angehoben werden.
Diese systembedingte Verteilung – manchmal als „Natural Slotting“ bezeichnet – funktioniert ohne separate Analyse oder Reorganisation.
Vorbereitende Bewegungen durch das System
Ein weiterer Effizienzfaktor liegt in der antizipierenden Arbeitsweise der Roboterflotte: Zwischen dem Eingang eines Kommissionierauftrags in der Lagerverwaltung und der tatsächlichen Bereitstellung am Port vergeht in der Regel etwas Zeit. AutoStore nutzt diese Zeitfenster, um vorbereitende Schritte einzuleiten – beispielsweise:
- Freilegen von tieferliegenden Bins, auf die bald zugegriffen werden muss
- Umstapeln von Bins, um den Weg zu priorisierten Artikeln freizumachen
- Vorpositionieren von häufig benötigten Artikeln in Nähe eines Ports
Diese vorbereitenden Abläufe helfen dabei, Zugriffszeiten zu reduzieren und Arbeitsplätze kontinuierlich mit Nachschub zu versorgen – ohne dass ein aktiver Lagerumbau notwendig ist. Gehen wir jetzt näher auf die einzelnen Module ein:
Das AutoStore-Grid: Fundament der Lagerautomatisierung
Aufbau und Funktion
Das Grid besteht aus Aluminiumprofilen, die eine Matrix aus Lagerplätzen für die Behälter schaffen. Die Roboter bewegen sich auf der obersten Ebene und haben über vertikale Hubvorrichtungen Zugriff auf die Behälter in den darunterliegenden Schächten. Die maximale Höhe ist abhängig von der Deckenhöhe, den Brandschutzvorgaben und der gewünschten Behälteranzahl.
Wichtiges über das Grid
- Modularität: Anpassbar in Höhe, Breite und Tiefe – ideal für Neubau und Retrofit
- Flächennutzung: Über 60 % höhere Lagerdichte als konventionelle Systeme
- Flexibilität: Erweiterungen im laufenden Betrieb möglich
- Skalierbarkeit: Vom Mikro-Grid bis zu Großanlagen mit mehreren tausend Quadratmetern
Besonderheiten
Ein zentrales Alleinstellungsmerkmal ist die Fähigkeit des AutoStore-Grids, dicht an bestehende Gebäudestrukturen heranzurücken – selbst Säulen oder Wände können elegant „umschlossen“ werden. Darüber hinaus kann das Grid mehrere Etagen überbrücken, wenn BinLifts integriert werden.
AutoStore kann grundsätzlich auch auf mehreren Ebenen installiert werden – sei es auf einem Zwischengeschoss oder als „doppelstöckige“ Grid-Lösung mit Port-Zonen auf verschiedenen Etagen. Technisch ist das realisierbar, insbesondere mithilfe von BinLifts, die Behälter vertikal zwischen den Ebenen transportieren können.
Doch warum wird das selten gemacht?
So attraktiv ein mehrgeschossiger Aufbau auf dem Papier wirkt – in der Realität scheitert er oft an wirtschaftlichen und statischen Herausforderungen.
Statische Anforderungen: Präzision und Tragfähigkeit
Damit ein AutoStore-System störungsfrei funktionieren kann, gelten vergleichsweise hohe Anforderungen an die Bodeneigenschaften, insbesondere bei Grids auf Zwischengeschossen:
Diese Anforderungen führen zu baulichem Aufwand bei Zwischengeschossen. Bühnen mit dieser Präzision und Tragkraft sind technisch realisierbar, aber teuer in Planung und Umsetzung.
Wirtschaftlichkeit: Wann lohnt es sich wirklich?
Ob ein mehrgeschossiger Aufbau sinnvoll ist, hängt stark vom Einzelfall ab:
- Vorteile:
- Flächennutzung bei geringer Grundfläche
- Einbindung in bestehende Gebäudestrukturen mit Etagen
Verbindung von Lager und Kommissionierung auf unterschiedlichen Ebenen
- Nachteile:
- Deutlich höhere Baukosten (Tragwerk, Statiknachweis, Spezialfundamente)
- Aufwendigere Montage
- Mögliche Einschränkungen bei der Skalierbarkeit
Also ja, AutoStore kann mehrgeschossig realisiert werden – aber es ist in der Praxis nicht immer wirtschaftlich sinnvoll. Die Kombination aus Traglast und Installationsaufwand kann potenzielle Anwendungen unwirtschaftlich machen.
Fazit zum Grid
Das Grid bildet nicht nur das physische Rückgrat des AutoStore-Systems, sondern ist auch ein maßgeblicher Faktor für die Lagerdichte, Energieeffizienz und Betriebssicherheit. Es erlaubt die Realisierung individueller Layouts, ohne Kompromisse bei Geschwindigkeit oder Skalierbarkeit einzugehen.
Die AutoStore-Behälter: Herzstück der Lagerung
Die sogenannten „Bins“ sind das zentrale Lagermedium innerhalb eines AutoStore-Systems. Sie dienen als Lagerbehälter für Artikel verschiedenster Art – von Kleinteilen über Komponenten bis hin zu Konsumgütern. Die Wahl der passenden Behälterhöhe beeinflusst unmittelbar die Lagerdichte, die Systemhöhe und die Auswahl des Robotertyps.
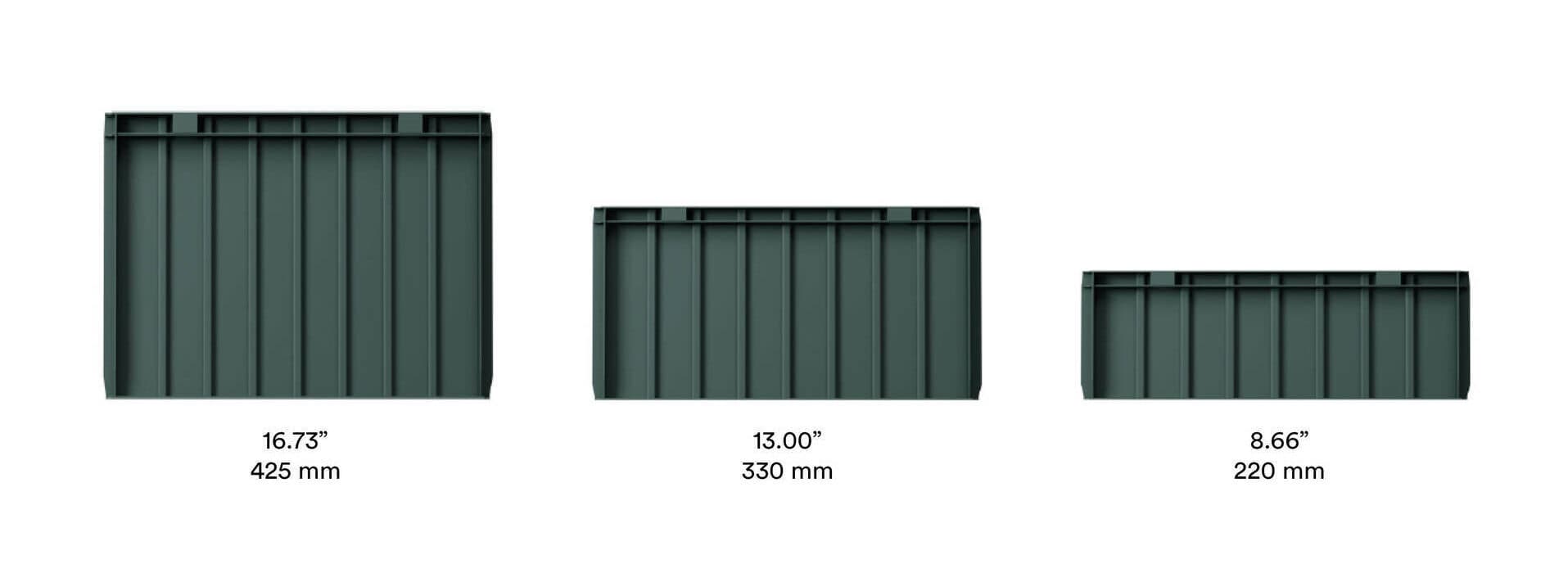
Varianten und Abmessungen
AutoStore bietet drei standardisierte Behältergrößen, die sich in der Höhe unterscheiden, aber dieselbe Grundfläche aufweisen:
Alle Behälter bestehen aus hochfestem Kunststoff (Polypropylen), sind stapelbar und verfügen über glatte Innenwände zur einfachen Reinigung und automatischen Vereinzelung.
Eigenschaften und Optionen
Die AutoStore-Behälter zeichnen sich durch zahlreiche funktionale und optionale Merkmale aus:
- Material: Die Behälter bestehen aus hochwertigem, schlagzähem Polypropylen (PP), das sowohl recycelbar als auch besonders langlebig ist. Das Material ist lebensmitteltauglich, chemikalienbeständig und leicht zu reinigen.
- Farbgebung: Standardmäßig werden die Bins in neutralen Farben wie Grau oder Anthrazit ausgeliefert.
- Zubehör & Innenorganisation: Optional sind verschiedene Inlays und Unterteilungen verfügbar – etwa Trenneinsätze für Sortimentslagerung oder textile Einsätze für empfindliche Produkte. Auch Schaumstoffeinlagen zur Stoßdämpfung können integriert werden.
- ESD-Ausführung: Für elektrostatisch sensible Produkte (z. B. Elektronikkomponenten) gibt es die Behälter auch in ESD-konformer Variante mit leitfähigem Kunststoff.
- Codierung & Tracking: Behälter können mit Barcodes oder 2D-Datamatrix-Codes versehen werden, um eine lückenlose Nachverfolgung im System zu ermöglichen. Diese Codes lassen sich sowohl aufgedruckt als auch in Form robuster Etiketten realisieren.
- Lebensdauer & Reinigung: Die glatten Innenflächen verhindern Verschmutzungen und erleichtern die regelmäßige Reinigung, auch automatisiert. Bei normalem Betrieb überstehen die Bins mehrere Millionen Bewegungszyklen.
Einfluss auf das Systemdesign
Bei der Systemauslegung muss man sich für einen Behältertypen entscheiden. Die gewählte Bin-Höhe hat direkten Einfluss auf:
- Die Höhe des Grids (Anzahl Stapel pro Turm)
- Den benötigten Robotertyp (nicht alle Roboter können 425er-Bins heben)
- Die Artikelvielfalt pro Behälter (abhängig von Größe & Aufteilung)
Warum keine Mischbestückung?
Ein häufiger Punkt in Diskussionen rund um AutoStore betrifft die Frage, warum man innerhalb eines Systems nicht verschiedene Behälterhöhen gleichzeitig nutzen kann. Was auf den ersten Blick wie eine Einschränkung erscheint, ist in der Praxis deutlich weniger problematisch – und hat gute systemtechnische wie auch mathematisch-logistische Gründe.
Das AutoStore-Grid basiert auf einer streng modularen Struktur mit klar definierten Rasterhöhen. Würde man verschiedene Behälterhöhen (z. B. Bin 220 und Bin 425) in einem Stack mischen, entstünden ungenutzte Zwischenräume und ein komplexeres Steuerungsverhalten für die Roboter.
Mathematische Überlegung
Nehmen wir als Beispiel ein Grid mit 6 möglichen Behälterebenen:
- Bei ausschließlich Bin 220 passen 6 Bins in einen Stack.
- Bei ausschließlich Bin 330 sind es 4 Bins.
- Bei ausschließlich Bin 425 nur 3 Bins.
Würde man nun Bins unterschiedlicher Höhen mischen, entstehen häufig Konstellationen, bei denen kein weiterer Behälter mehr obenauf passt, obwohl rechnerisch noch „ein bisschen Platz“ vorhanden wäre. Dieses Restvolumen bleibt ungenutzt – die Packungsdichte sinkt. Die Lagerdichte ist damit bei homogener Behälterverwendung effizienter.
Praxisorientiertes Design
Statt eine Mischnutzung innerhalb eines Grids zu erzwingen, setzen Unternehmen auf systematische Trennung:
- Man entscheidet sich komplett auf eine einheitliche Behälterhöhe
- Oder unterschiedliche Systeme (bzw. Grids) kommen für verschiedene Artikelgruppen zum Einsatz.
Fazit zu den Behältern
Die AutoStore-Behälter sind nicht nur einfache Lagerboxen, sondern eine zentrale Systemkomponente. Sie bestimmen maßgeblich das Lagervolumen pro Quadratmeter, die Auswahl der Roboter sowie die Effizienz bei der Kommissionierung. Eine sorgfältige Auswahl unter Berücksichtigung von Artikelstruktur, Pickingstrategie und Nachschublogik ist daher essenziell.
AutoStore Roboter im Überblick: Leistung, Unterschiede und Bedeutung
Die Roboter sind das Herzstück des AutoStore-Systems – sie bewegen sich auf dem Grid, heben Behälter an, stapeln sie um und bringen sie zu den Ports. Dabei übernehmen sie alle vertikalen und horizontalen Bewegungen oberhalb des Behälterlagers. In der aktuellen Generation existieren verschiedene Robotermodelle, die sich hinsichtlich Dimensionen, Geschwindigkeit, Tragkraft und Energieeffizienz unterscheiden.
R5™
Der Klassiker unter den AutoStore-Robotern. Über viele Jahre hinweg der Standard in zahlreichen Projekten – robust, zuverlässig und kosteneffizient.
R5+™
Weiterentwicklung des R5 mit Fähigkeit, auch größere Behälter (bis 425 mm Höhe) zu transportieren.
R5 Pro™
Der effizienteste Roboter der R5-Reihe, mit Li-Ion-Batterie, entwickelt für große Systeme und lange Einsatzzeiten.
R5+ Pro™
Vereint die Vorteile von R5+ (größere Behälter) und R5 Pro (Schnellladung) in einem leistungsfähigen Modell.
Vergleichstabelle der AutoStore-Roboter
Fazit zu den Robotern:
Für die Auswahl des passenden Robotertyps im AutoStore-System sind nicht primär die technischen Unterschiede entscheidend, sondern die betrieblichen Rahmenbedingungen des Unternehmens. Aspekte wie Durchsatzanforderung, Schichtbetrieb, verfügbare Fläche und Energieeffizienz spielen hierbei eine größere Rolle. Die Entscheidung für ein bestimmtes Robotermodell – sei es R5 oder R5+, Pro oder nicht-Pro – wird in der Regel vom Integrator im Rahmen der Konzeptionsphase getroffen. Für den Endanwender ist letztlich weniger relevant, welches Modell auf dem Grid fährt, solange das System als Ganzes die gewünschten Leistungsparameter erfüllt.
AutoStore Ports im Vergleich: Schnittstelle zwischen Roboter und Mensch
Die Ports – also die Arbeitsstationen, an denen Behälter ein- oder ausgelagert werden – sind zentrale Komponenten des AutoStore-Systems. Sie fungieren als Schnittstelle zwischen dem automatisierten Lagersystem und den Mitarbeitenden (bzw. Kommissionierrobotern) und bestimmen zu einem großen Teil die Leistungsfähigkeit des Gesamtsystems. Je nach Anwendungsfall, Durchsatzanforderung und Ergonomieaspekten stehen unterschiedliche Port-Typen zur Auswahl:
ConveyorPort™
Der einfachste und kompakteste Port. Die Übergabe erfolgt direkt vom AutoStore Roboter auf ein Förderband. Diese Arbeitsstation kann durch den geringen Platzbedarf sehr gut für Prozesse mit höheren Handling Zeiten (bspw. im Wareneingang) genutzt werden.
VersaPort™
Ein modularer Arbeitsplatz mit Sicherheitsklappe, ideal für einfache Lagerprozesse oder zur Kombination mehrerer Ports nebeneinander. Der VersaPort stellt eine Weiterentwicklung des ConveyorPorts dar.
SwingPort™
Ein spezieller Port für mehrstöckige Gebäude, da er Behälter zwischen Etagen befördern kann.
CarouselPort™
Einer der beliebtesten Ports, ausgestattet mit drei rotierenden Armen zur Pufferung der Behälter.
FusionPort™
Ein ergonomischer Hochgeschwindigkeitsarbeitsplatz, der speziell auf Effizienz und Bedienkomfort ausgelegt ist.
RelayPort™
Der leistungsstärkste Port im Portfolio. Zwei vertikale Fördereinheiten sorgen für minimale Wartezeiten.
FusionPort Staging™
Ergänzung zum FusionPort mit Möglichkeit zur Zwischenlagerung. Ideal für das sequentielle Kommissionieren und Pufferungen von Teilaufträgen.
PickUpPort™
Ein für den Endkunden konzipierter Port, der eine direkte Abholung von Waren im Laden oder an einem Ausgabeautomaten ermöglicht.
Vergleichstabelle der AutoStore-Porttypen:
Zusätzlich zu den genannten Port-Typen werden sogenannte Transferzellen für die Anbindung von Fördertechnik genutzt. Hierbei werden Bins auf eine physikalische Position abgestellt bzw. von dort aufgenommen.
Fazit zu den AutoStore-Ports:
Die Wahl des richtigen Port-Typs hat unmittelbaren Einfluss auf die Leistung und Effizienz eines AutoStore-Systems. Während CarouselPorts als Allrounder gelten, bietet der RelayPort Spitzenleistung für anspruchsvolle Anwendungen. Entscheider sollten Porttypen stets im Zusammenspiel mit dem erwarteten Auftragsprofil, Ergonomieanforderungen und Kommissionierstrategie auswählen, denn die angegebenen Durchsatzwerte stellen lediglich technische Maximalwerte unter Idealbedingungen dar. Eine ganzheitliche Betrachtung der Prozesskette rund um den Port ist daher entscheidend.
Der AutoStore Controller: Hirn der Anlage
Die Rolle des Controllers
Der AutoStore Controller ist eine speziell entwickelte Softwarelösung, die:
- alle Roboterbewegungen in Echtzeit steuert,
- Kollisionsvermeidung gewährleistet,
- Ports mit Robotern synchronisiert,
- Aufträge priorisiert und Puffervorgänge optimiert,
- Ausfallstrategien und Redundanzen verwaltet.
Er verarbeitet dabei hunderttausende Rechenoperationen pro Sekunde, um das Optimum an Durchsatz, Energieeffizienz und Systembalance zu gewährleisten.
Wichtiger als die Hardware
So beeindruckend das mechanische System auch ist: Die eigentliche Leistungsfähigkeit liegt in der Software. Der Controller entscheidet, wann welcher Roboter welchen Bin bewegt – abhängig von Auftragslage, Warteschlangen, Behälterposition und Portverfügbarkeit. Selbst bei mehreren Tausend Bewegungen pro Stunde entstehen so keine Kollisionen.
Abgrenzung zum WCS
Der AutoStore Controller ist kein klassisches Warehouse Control System (WCS). Er agiert ausschließlich innerhalb des AutoStore-Kerns und kennt keine Artikelinformationen, Kundenaufträge oder Lagerstrategien im ERP-Sinn. Diese Aufgaben übernimmt das WCS, das vom jeweiligen Systemintegrator oder einem Drittanbieter bereitgestellt wird.
Typische Funktionen des WCS:
- Kommissionierstrategie (z. B. FIFO, Batch, Prioritäten)
- Konsolidierung und Sortierung
- Steuerung von Fördertechnik außerhalb AutoStore
- Kommunikation mit übergeordneter Lagerverwaltung (WMS) oder ERP
Der Controller kommuniziert über definierte Schnittstellen (REST API, TCP/IP) mit dem WCS, erhält daraus Aufträge und sendet Statusinformationen zurück.
Fazit zum Controller
Der Controller ist das „Gehirn“ eines AutoStore-Systems. Zwar bleibt er physisch und visuell im Hintergrund, doch ohne ihn wäre keine intelligente Steuerung der Anlage möglich. In der Gesamtkonzeption ist deshalb nicht nur die Hardware entscheidend – sondern vor allem die Softwarearchitektur und deren Zusammenspiel mit dem übergeordneten WCS.
Erfolgsfaktor Planung: Was man vor der Einführung eines AutoStore-Systems beachten sollte
Die Einführung eines AutoStore-Systems ist kein Plug-and-Play-Projekt – auch wenn das Systemkonzept standardisiert wirkt, ist jede Anlage individuell zu planen. Die besten Ergebnisse entstehen dort, wo die Planung nicht rein auf Basis der Technik erfolgt, sondern ganzheitlich prozessorientiert, datengestützt und zukunftsgerichtet.
1. Artikelstruktur & Lagerstrategie analysieren
Ein AutoStore-System funktioniert ideal, wenn die Artikel:
- eine gewisse Standardverpackung oder Behälterverträglichkeit aufweisen,
- klein bis mittelgroß sind (Hier muss auch auf das Gewicht geachtet werden.)
Produkte mit Übergröße, komplexer Struktur oder starker Verschmutzungsneigung eignen sich dagegen weniger. Eine strukturierte Analyse der Stammdaten, Gewichtsklassen und Zugriffsfrequenzen ist daher essenziell.
2. Durchsatzanforderung und Taktzeit kalkulieren
Die notwendige Leistungsfähigkeit eines AutoStore-Systems hängt stark vom Auftragsprofil ab:
- Anzahl Picks pro Stunde
- Verteilung über Schichten und Wochentage
- Anteil an Einzel- vs. Sammelaufträgen
- Retourenquote, Wareneingangszyklen
Erst diese Daten zeigen, wie viele Roboter und Ports benötigt werden – und ob ein System wirtschaftlich skalierbar ist.
3. IT- und Schnittstellenkonzept frühzeitig definieren
AutoStore ist ein System ohne eigene Artikelverwaltung. Alle Bewegungen müssen vom übergeordneten WCS oder WMS angestoßen und verarbeitet werden. Deshalb sind klare IT-Anforderungen früh zu klären:
- Ist ein WCS vorhanden? Oder soll es über den Integrator kommen?
- Wie erfolgt die Integration in SAP, Navision oder andere ERP-Systeme?
- Welche Prioritäten gelten bei Mehrfachaufträgen, Eilfällen oder Nachschub?
Auch Aspekte wie Benutzerrollen, Dashboards, Monitoring und API-Performance gehören zur frühen IT-Planung.
4. Bauliche Rahmenbedingungen realistisch prüfen
Wie hoch ist die Halle? Gibt es Säulen oder Sprinklerköpfe, die Layout oder Portpositionen einschränken? Ist der Boden ausreichend eben und tragfähig (Stichwort FF/FL-Werte)?
Diese Fragen entscheiden über:
- mögliche Gridhöhe und -fläche
- Positionierung von Ports (auch SwingPorts über Etagen)
- Montageaufwand und Baustellenlogistik
5. Wachstum & Flexibilität mitdenken
Ein AutoStore-System ist skalierbar – aber nur, wenn die Rahmenbedingungen dafür geschaffen wurden:
- Reserveflächen im Layout
- Stromversorgung für zusätzliche Ports und Roboter
- IT-Infrastruktur auf Mehrleistung ausgelegt
- Modulare WMS-Anbindung
Wer heute schon Expansion mitdenkt, vermeidet spätere Umbaukosten.
6. Projektlaufzeit & Implementierung: Von der Idee zum Go-Live
Die Einführung eines AutoStore-Systems verläuft nicht über Nacht – auch wenn viele Komponenten standardisiert sind, ist der Planungs- und Implementierungsprozess intensiv. Eine realistische Einschätzung der Projektlaufzeit hilft, Ressourcen zu planen und intern tragfähige Erwartungshaltungen zu etablieren.
Typische Projektphasen:
- Vorstudie & Konzeptphase (4–8 Wochen)
- Analyse von Artikelstruktur, Durchsatz, Prozessen
- Erstellung eines Groblayouts
- Auswahl von Integrator & Angebotsphase
- Detailplanung & Vertragsabschluss (4–6 Wochen)
- Abstimmung zu Brandschutz, IT, Portpositionen, Ausbaustufen
- Definition von Schnittstellen (WMS/WCS)
- Produktion & Lieferung (8–14 Wochen)
- Grid-Produktion, Roboterlieferung, Ports, Steuerung
- Parallel: Baustellenvorbereitung, Bodenprüfung, Statikfreigabe
- Montage & Inbetriebnahme (4–8 Wochen)
- Grid-Aufbau, Portmontage, IT-Anbindung, Tests
- Go-Live & Ramp-up (2–6 Wochen)
- Mitarbeiterschulung, Datenanbindung, Performance-Optimierung
Gesamtzeit: Ø 5 bis 8 Monate
Je nach Komplexität, Bauphase und IT-Reifegrad variiert die Projektlaufzeit zwischen 5 und 12 Monaten. Eine realistische Planung hilft dabei, Go-Lives terminsicher zu realisieren.
7. Typische Fehler und Best Practices aus AutoStore-Projekten
Auch wenn AutoStore modular und „einfach“ wirkt – viele Projekte kämpfen mit typischen Fallstricken, die sich mit guter Vorbereitung vermeiden lassen:
8. Was bei der AutoStore-Planung wirklich gefordert ist – aus Sicht echter Ausschreibungen
Viele AutoStore-Projekte starten nicht mit einem simplen Lastenheft, sondern mit umfangreichen Ausschreibungen (RFI/RFQ/RFP), in denen Unternehmen ihre Anforderungen an Technik, IT, Ergonomie, Layout und Betrieb sehr konkret definieren. Die Analyse solcher Dokumente zeigt, welche Punkte in der Praxis besonders häufig und detailliert gefordert werden – und wo integrative Planung essenziell ist.
Zentrale Planungsanforderungen aus typischen Ausschreibungen
Wer eine AutoStore-Anlage plant, muss weit mehr beachten als Lagerplätze und Roboterzahl. Die reale Ausschreibungspraxis zeigt: Kunden erwarten durchdachte, skalierbare, ergonomische und dokumentierte Lösungen – technisch wie organisatorisch. Wer hier mit Standardannahmen agiert, wird in späteren Phasen oft teuer nacharbeiten müssen. Deshalb lohnt es sich, von Beginn an integrativ zu denken: von Gebäudetechnik über Prozesse bis zu User Experience und Wartung.
Dabei ist es nicht zwingend erforderlich, ein vollumfängliches RFI-, RFQ- oder RFP-Verfahren durchzuführen. Viel entscheidender ist, dass projektrelevante Daten wie Artikelstruktur, Auftragsprofile, Lagerkennzahlen und Layoutrestriktionen frühzeitig in strukturierter Form vorliegen. Nur so kann ein belastbares und vergleichbares Konzept erarbeitet werden – unabhängig davon, ob der Prozess formal ausgeschrieben oder partnerschaftlich entwickelt wird.
Kostenstruktur eines AutoStore-Projekts: Was kostet wie viel?
Ein AutoStore-System erscheint auf den ersten Blick modular und standardisiert – bestehend aus Grid, Robotern, Behältern, Ports, Controllern und Software. Doch die Realität ist deutlich komplexer: Eine Analyse von über 20 realen Kundenangeboten aus Europa und Nordamerika zeigt, dass sich die tatsächlichen Projektkosten erheblich unterscheiden – abhängig von Faktoren wie Durchsatzanforderungen, baulichen Gegebenheiten, Layout, Automatisierungsgrad und IT-Integration.
Typische Kostenverteilung im AutoStore-Projekt (branchenübliche Erfahrungswerte)
Auffälligkeiten & Muster aus realen Projektangeboten
Die Analyse zeigt, dass sich hinter den Zahlen bemerkenswerte Unterschiede und Planungsansätze verbergen:
- Roboterflotten variieren stark je nach Durchsatz, Auftragsstruktur und Grid-Layout: In einem Projekt mit 400 Picks/h reichten 35 Roboter, in einem anderen mit 850 Picks/h wurden 62 Roboter plus 8 Charger kalkuliert. Dabei zeigt sich: Nicht allein der Ziel-Durchsatz bestimmt die Flottengröße, sondern auch die Art der Aufträge (z. B. Multiline- oder Ein-Artikel-Kommissionierung), die geografische Verteilung der Ports und die Form des Grids. Pauschale Annahmen oder reine Rechenmodelle auf Basis von Bins/h führen daher häufig nicht zu einem realistischen Ergebnis – Simulationen auf Basis echter Auftragsdaten sind deutlich präziser.
- Grid-Kosten beziehen sich ausschließlich auf das Aluminiumraster des AutoStore-Systems: Zusätzliche bauliche Maßnahmen wie Zwischengeschosse, Traggerüste oder Verstärkungen für Brandschutzauflagen (z. B. abgehängte Sprinkler, Löschanlagen, Rauchmelder) fallen unter separate Kostenpositionen und sollten nicht in die Grid-Kalkulation einfließen. Mehrere Angebote zeigen, dass gerade diese baulichen Zusatzmaßnahmen – insbesondere bei mehrgeschossiger Nutzung – den Stahlbau- und Brandschutzaufwand um bis zu 60 % erhöhen können. Sie sollten als eigenständige Position in der Projektplanung betrachtet werden.
- Bin-Kosten sind konstant kalkulierbar, aber preissensibel: Ein Integrator nennt explizit die Bindung der Preise an den Kunststoffpreisindex. Zusätzlich sollte insbesondere die Lieferung der Behälter nicht unterschätzt werden – je nach geografischer Lage des Projekts können hier erhebliche Logistikzuschläge anfallen. Die Behälter selbst stammen nicht direkt von AutoStore, sondern werden von zertifizierten Drittanbietern gefertigt und zugeliefert, was sich positiv auf Verfügbarkeit und Preisstabilität auswirkt, aber auch abhängig von Transportwegen und Lieferkapazitäten ist.
- Ports sind der strategische Hebel für Pickleistung – aber auch teuer: Die Wahl zwischen z. B. einem ConveyorPort (Basislösung), einem RelayPort (automatisierter Transfer) und einem FusionPort (gleichzeitiger Pick/Put) hat direkten Einfluss auf Budget und Prozessgeschwindigkeit. RelayPorts lagen in manchen Angeboten fast doppelt so hoch wie einfache Ports. Besonders deutlich wird der Unterschied beim Vergleich von FusionPort und CarouselPort: Während der CarouselPort als bewährte Standardlösung mit geringem Platzbedarf und einfacher Integration gilt, bietet der FusionPort die Möglichkeit, Einlagerung und Auslagerung gleichzeitig durchzuführen – was den Durchsatz erheblich erhöht. Dieser technologische Vorteil spiegelt sich jedoch auch im Preis wider: In mehreren Angeboten lag der Preis eines FusionPorts etwa 60–80 % über dem eines CarouselPorts. Dafür lässt sich in der Regel eine deutlich höhere Pickfrequenz von 450–500 Picks/h gegenüber rund 250–300 Picks/h beim CarouselPort erreichen. Projekte mit sehr hohen Performance-Anforderungen, konzentrierten Auftragsprofilen oder zentralisierten Kommissionierbereichen profitieren daher vom Einsatz des FusionPorts – sofern der Budgetrahmen das hergibt. Für klassische Lageranwendungen mit moderatem Volumen, dezentraler Struktur und niedrigeren Taktanforderungen stellt der CarouselPort die wirtschaftlichere Wahl dar.
- Software & Steuerung selten sauber aufgeschlüsselt: Viele Angebote bündeln ACS, Middleware, Alarmsysteme und teilweise auch WMS-Anbindung in einer Gesamtsumme. Eine genaue Prüfung der enthaltenen Leistungen ist hier unerlässlich.
- Fördertechnik ist kein Standard, sondern Layout-abhängig: Während manche Projekte gänzlich ohne auskommen (z. B. manuelle Kommissionierung direkt an Ports), enthalten andere komplette Versandlinien mit Sortierung, Übergabe und Puffern – mit Kostenanteilen von über 20 %.
Fazit: Die echten Kostentreiber liegen in der Planung
Die Preisstruktur eines AutoStore-Systems lässt sich nicht pauschal aus dem Katalog ableiten. Vielmehr ergibt sich das Gesamtbild aus zahlreichen strategischen, baulichen und technischen Faktoren:
- Welche Leistung muss das System täglich oder stündlich erbringen?
- Welche Artikelstruktur, Zugriffshäufigkeit und Lagerreichweite soll abgebildet werden?
- Wie lassen sich Ports optimal integrieren und ergonomisch platzieren?
- Wie komplex ist die IT-Landschaft? Gibt es bestehende Schnittstellen oder wird neu integriert?
- Welche behördlichen Auflagen (z. B. Brandschutz, FM Global) beeinflussen das Layout?
Je konkreter diese Fragen vor Projektstart beantwortet werden können – etwa durch Datenanalyse, Simulation oder Workshops – desto effizienter und planbarer wird die Umsetzung. Ein direkter Angebotsvergleich zweier Projekte mit ähnlicher Lagerfläche, aber unterschiedlicher Portanzahl und IT-Anforderungen, zeigte Preisunterschiede von über 25 %.
Tipp: Schon in der Konzeptionsphase lohnt sich der enge Austausch mit erfahrenen Systemintegratoren. Ein guter Partner zeigt nicht nur eine einzelne Systemlösung auf, sondern entwickelt mehrere Varianten, prüft deren Machbarkeit, simuliert reale Lastszenarien und bewertet die Auswirkungen auf Kosten, Leistung und Flexibilität. So lassen sich realistische Layouts, Leistungskennzahlen und Budgets frühzeitig definieren – was in der späteren Umsetzung wertvolle Zeit spart, Kosten senkt und nachträgliche Anpassungen vermeidet.
Verteilung der Kosten – ein Blick auf die typischen Projektanteile
Auch wenn jedes AutoStore-Projekt individuell geplant wird, lassen sich aus realen Angeboten klare Tendenzen erkennen: Den größten Anteil am Gesamtbudget nehmen in der Regel die Roboter ein, gefolgt vom Grid und den Ports. Auffällig ist außerdem, dass Fördertechnik und IT-Integration je nach Projekt stark variieren – je komplexer das Umfeld, desto höher die entsprechenden Kosten. Andere Positionen wie Controller, Montage oder Sonderposten sind stabiler und lassen sich in frühen Planungsphasen meist gut abschätzen. Die nachfolgende Grafik zeigt eine durchschnittliche Kostenverteilung auf Basis von über 20 ausgewerteten AutoStore-Angeboten.
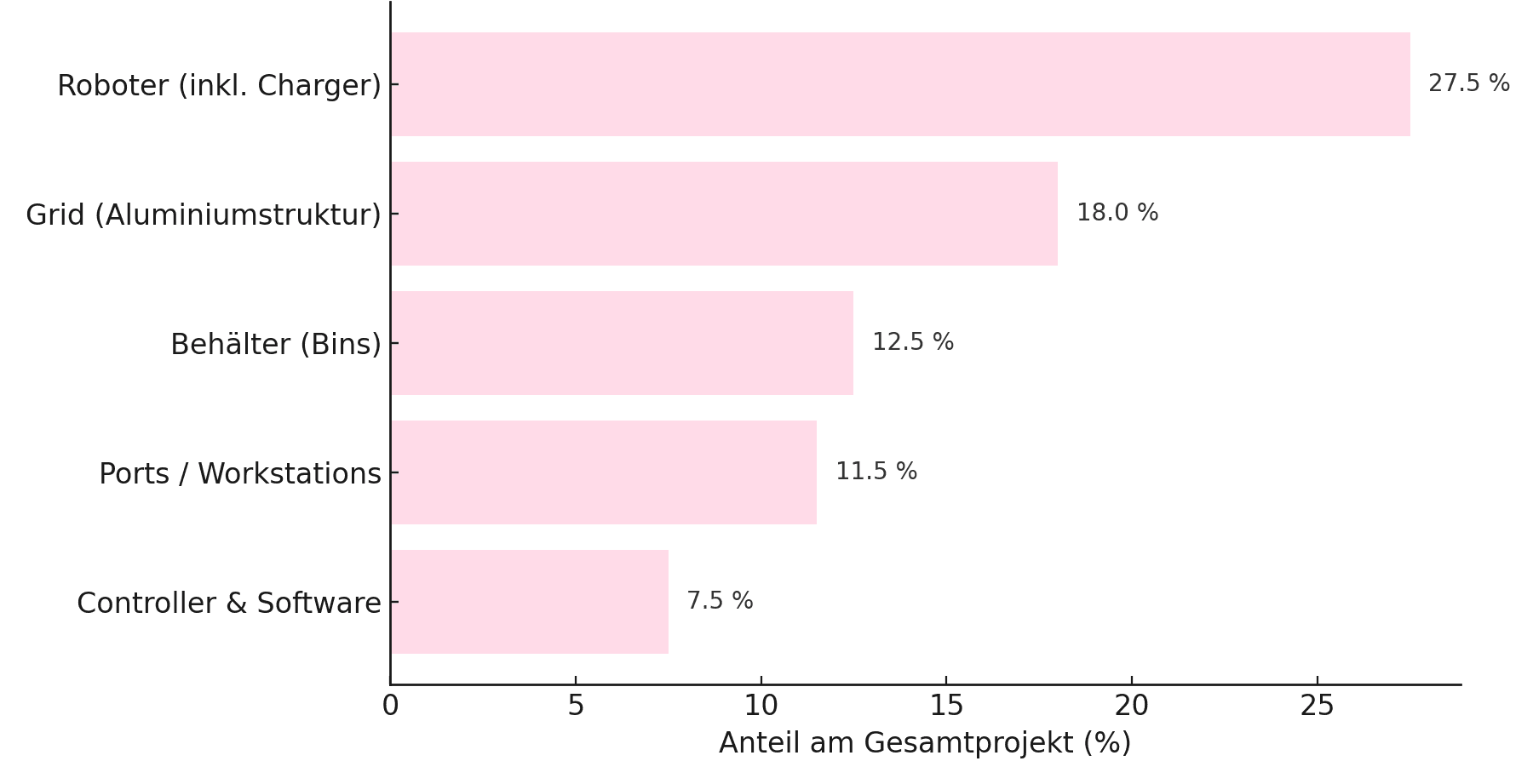
Hinweis: Die prozentualen Angaben basieren auf Erfahrungswerten und dienen der Orientierung. In der Praxis können die Anteile einzelner Komponenten je nach Projektgröße, Layout, Durchsatzanforderung und Integrationsgrad stark variieren. Die Übersicht zeigt ausschließlich die Kernmodule des AutoStore-Systems – bauliche Maßnahmen, WCS-Software, IT-Anbindung und weitere Nebenkosten sind nicht berücksichtigt.
Brandschutz im AutoStore-System: Anforderungen, Konzepte und Praxis
Der Brandschutz ist ein zentrales Thema bei der Planung und Genehmigung automatisierter Lagersysteme – insbesondere bei dichten, geschlossenen Systemen wie AutoStore. Durch die kompakte Bauweise und die hohe Lagerdichte ergeben sich besondere Anforderungen an Detektion, Eindämmung und Kommunikation mit Behörden.
Grundlagen: AutoStore ist ein geschlossenes System
Ein AutoStore-System besteht aus einem engmaschigen Aluminium-Grid mit Kunststoffbehältern, auf dem Roboter agieren. Offene Flammenquellen existieren nicht. Dennoch müssen gesetzliche und versicherungstechnische Anforderungen erfüllt werden – abhängig von:
- der Lagergutart (brennbar, kritisch, klassifiziert)
- der Gebäudehöhe und Bauweise
- nationalen Vorschriften (z. B. MBO, VdS, FM Global)
AutoStore-Brandschutzkonzepte im Überblick
AutoStore selbst bietet keine integrierte Löschtechnik – die Brandschutzkonzepte werden stets standortspezifisch und projektspezifisch umgesetzt. Typische Schutzmaßnahmen sind:
- Frühzeitige Branddetektion: Einsatz von punktuellen Rauchmeldern, linearen Rauchansaugsystemen (RAS) oder Thermodetektionssystemen oberhalb und innerhalb des Grids.
- Rauch- und Wärmeabzug: Integration von Rauchabzugsklappen, insbesondere bei Deckeneinbauten.
- Sprinklerung: Bei manchen Anlagen ist eine flächendeckende oder zonierte Sprinklerung oberhalb des Grids notwendig – mit VdS-/FM-konformen Düsen.
- Inertisierung (Stickstoff): In besonders schützenswerten Bereichen kann das Grid in einem Bereich mit niedriger Sauerstoffkonzentration betrieben werden.
- Brandlastminimierung: Verwendung schwer entflammbarer Behältermaterialien (z. B. nach UL 94 HB) und strikte Ausschlussregeln für feuergefährliche Güter.
Anforderungen an Dokumentation & Genehmigung
Für jedes AutoStore-Projekt ist ein individuelles Brandschutzgutachten erforderlich. Dieses muss:
- die Art der Lagergüter und Gefahrstoffklassen definieren,
- technische Schutzmaßnahmen nachvollziehbar darstellen,
- mit den lokalen Behörden abgestimmt werden (z. B. Feuerwehr, Bauamt).
AutoStore stellt dafür eine standardisierte Dokumentation bereit, u. a. mit:
- Anforderungen an Bodenebenheit & statische Werte
- technischen Richtlinien für Brandschutz & RAS-Anbindung
- Empfehlungen für Wartung und Notabschaltung
Fazit zum Brandschutz
Brandschutz im AutoStore ist kein Hindernis – aber, wie in so ziemlich jedem Automatisierungsprojekt, ein zentraler Planungsbestandteil. In enger Abstimmung mit Bauaufsicht, Brandschutzgutachter und dem Systemintegrator lassen sich wirtschaftliche und sichere Lösungen realisieren. Eine frühzeitige Einbindung aller Akteure reduziert Risiken, Kosten und Genehmigungsdauer erheblich.
AutoStore-Systemintegratoren: Partnernetzwerk und ihre Rolle
AutoStore verfolgt ein indirektes Vertriebsmodell: Die Systeme werden nicht direkt vom Hersteller verkauft oder implementiert, sondern ausschließlich über zertifizierte Systemintegratoren realisiert. Diese Partner spielen eine zentrale Rolle im gesamten Lebenszyklus eines AutoStore-Projekts – von der Beratung und Systemauslegung über die Inbetriebnahme bis hin zu Service und Support.
Aufgaben der Integratoren:
- Konzeptionierung: Analyse von Durchsatz, Artikelstruktur, Pickprozessen und Flächenlayout
- Systemdesign: Auswahl der passenden Komponenten (Roboter, Ports, Grid-Geometrie)
- Implementierung: Projektmanagement, Montage, Schnittstellenanbindung
- Service & Wartung: 24/7-Support, Ersatzteile, Monitoring, SLA-basierte Betreuung
Auswahl eines geeigneten Partners
Jeder AutoStore-Integrator hat eigene Branchenschwerpunkte, technologische Ausprägungen und Erfahrungswerte. Bei der Auswahl eines Partners sollten Entscheider auf folgende Aspekte achten:
- Erfahrung in vergleichbaren Projekten (Branche, Größenordnung)
- IT-Kompetenz (WMS-Integration, SAP-Konnektivität)
- Servicekonzept & Reaktionszeiten
- Ergänzende Technologien (z. B. Fördertechnik, Robotik, Sorter)
- Skalierbarkeit und internationale Präsenz
Alle offiziellen AutoStore-Partner weltweit (Stand 2025)
Vergleichstabelle AutoStore-Integratoren
Fazit zum Integrator-Modell
Die enge Zusammenarbeit mit dem passenden Integrator ist für den Erfolg eines AutoStore-Projekts essenziell. Zwar liefert AutoStore die standardisierten Hardwarekomponenten, doch die Ausprägung, Integration und langfristige Betreuung unterscheiden sich je nach Partner deutlich. Daher sollte die Partnerwahl mit ebenso viel Sorgfalt erfolgen wie die Systementscheidung selbst.
FAQ: Häufige Fragen zum AutoStore-System
Auf der Suche nach einer passenden Lösung für deine Logistik? Hier geht's zur Vergleichsplattform, die dir die Suche erleichtert.